The global HMI market was valued at three billion euros in 2020 and is expected to reach a value of more than seven billion euros by 2026. It is expected to bring a number of added benefits to a facility in terms of safety, operations and production. HMI is expected to reduce operating costs by replacing traditional push buttons, indicator lights and selector switches and reduce the requirement for panels and further improve machine monitoring.
The importance of user interfaces has become increasingly clear in recent years. Many industrial corporations have come to the conclusion to focus more on the quality of the user interfaces of their products. Higher levels of functionality, as well as multi-touch screens and high-quality displays, are expected to drive market growth.
HMIs, in combination with PLCs, are the mainstay of the production line in various industries, greatly improving operations and enabling supervisory control and data acquisition throughout the system, making parameter changes possible according to the operator’s choice. For example, when processing metal, the HMI can control the method and speed at which a metal is cut and bent.
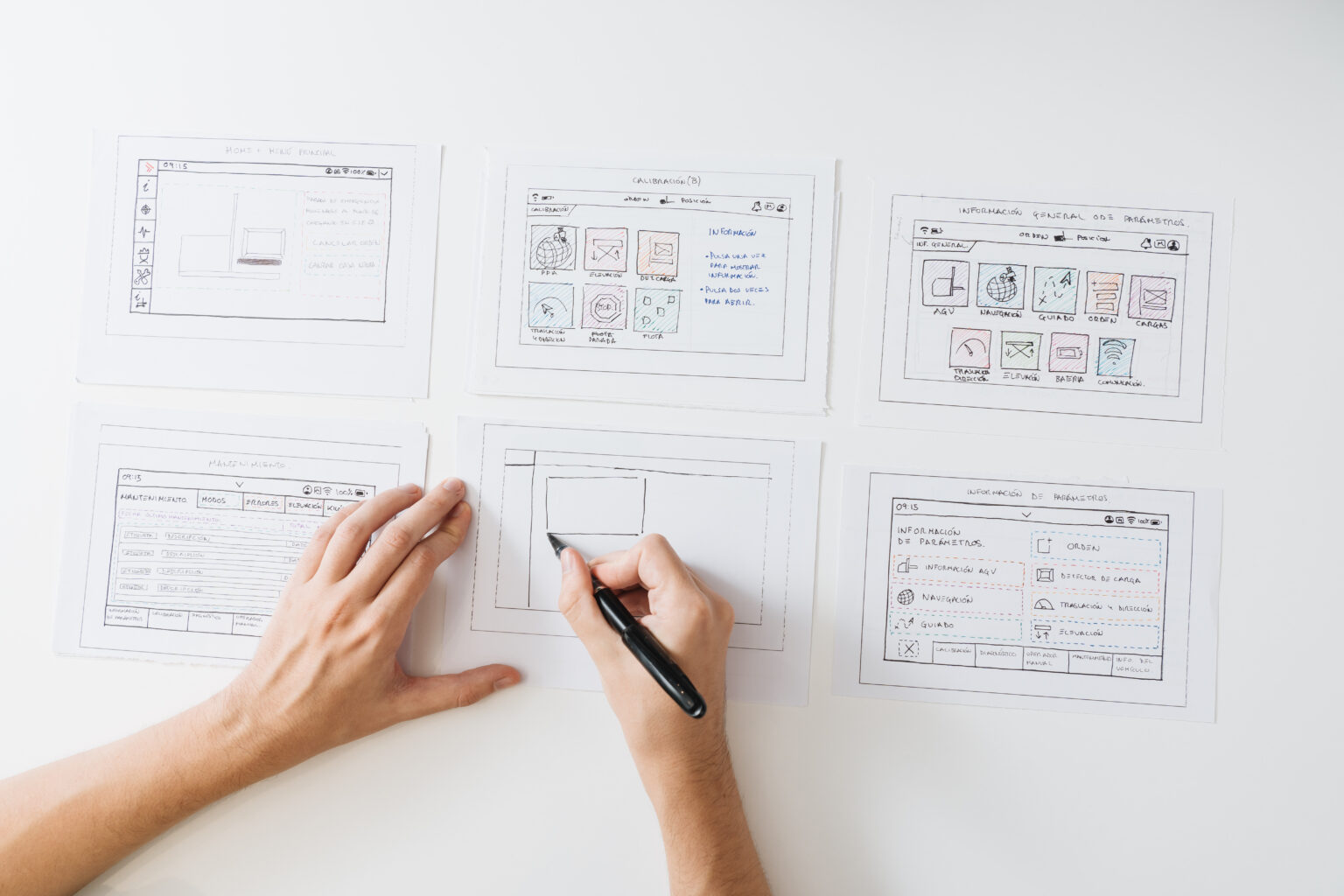
On the other hand, the importance of IoT should be highlighted. According to the World Bank, the number of IoT-connected devices is expected to reach more than 51,000 by 2023, so the need for HMIs to become more sophisticated is growing. In addition, the rise of Industry 4.0 and the Industrial Internet of Things (IIoT) has made this more accessible, increasing its accessibility and ease of use.
Advanced HMI, and its unconditional support for workers, is a reality. Where monitoring and control of plant information has long been done by operators working with fixed PCs, installed inside control rooms offering limited functionality, the reality is now very different. Employees have greater high-performance mobility, laptops and mobiles, giving workers the power, freeing them from being tied to the control room and allowing them to manage operations and troubleshoot problems in the field or on the shop floor. While some applications may require a fixed HMI, a large number of them may already be mobile. For example, if the operator requires maintenance assistance, he can contact other operators via the mobile HMI and work together to solve the problem.
And a complement that should be highlighted is Augmented Reality, which is redefining the human-machine interface. AR technology is introduced to enhance the user’s physical environment with computer-generated content. By integrating AR (Augmented Reality) it is possible to add real-time information to the environment, which is extremely useful for assessing current circumstances in order to improve decision making. This complementary audiovisual information is provided by electronic or computer-generated devices.
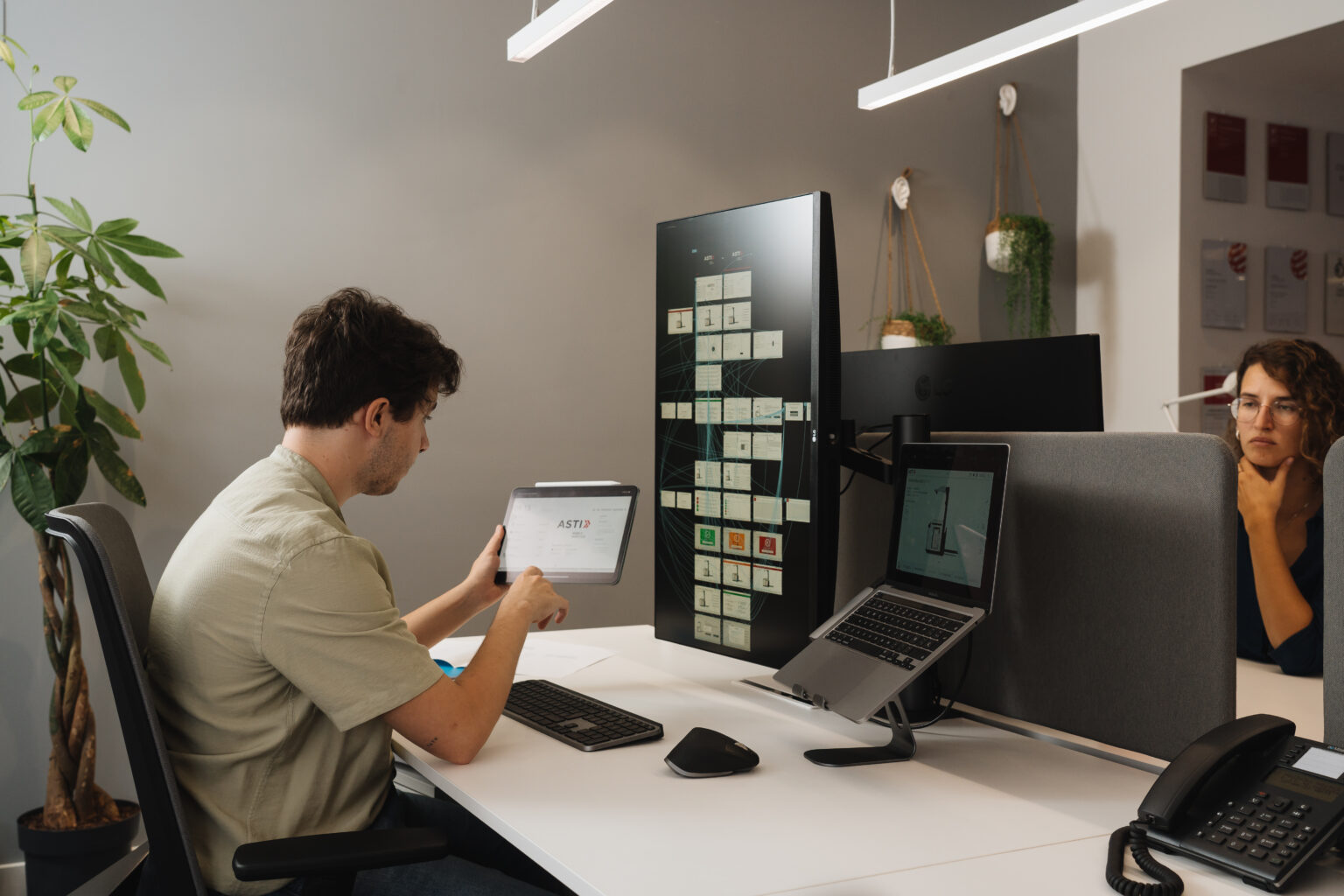
RA is suitable for both manufacturing and process industries, and allows the necessary actions to be taken at different stages, improving production efficiency, reducing errors and minimising production or maintenance downtime. In addition, it allows operators to be informed at the moment of any problem or need that may arise in the plant. Because receiving relevant information in real time and performing step-by-step guided operations and configurations directly on site is the cornerstone.
The AR device connects to the PC with Wifi, which manages the monitoring system, to which the field devices are connected. The devices usually come in the form of a kit, which includes glasses or helmets equipped with displays, cameras and audio equipment. The device’s screen can display real-time dynamic information relevant to the task at hand as well as process data, system status, alerts, actions required according to the work to be performed and other useful information. And depending on the alerts, operators can trigger the necessary commands, such as start, stop, modifications and alert-based instructions. As technology advances, AR systems tend to be complementary solutions, they will never replace traditional work process workstations, but it is true that the “hands-free” option offers much more flexibility and speed during operational phases than is possible with standard systems. AR and mixed reality systems simplify operational activities, providing a solution that integrates seamlessly with monitoring technologies.